The Design And Assembly Process Of Plastic Injection Mold Assembly In Manufacturing
Plastic injection mold assembly is a crucial process in the manufacturing industry. It involves the assembly of various components to create a mold that is used for injecting molten plastic into a desired shape. This process is essential for producing a wide range of plastic products, from small consumer goods to large industrial parts.
The importance of plastic injection mold assembly cannot be overstated. It is the foundation of the entire manufacturing process, as it determines the quality and precision of the final product. A well-assembled mold ensures that the injected plastic material is accurately shaped and free from defects. Without proper assembly, the final product may have imperfections or may not meet the required specifications.
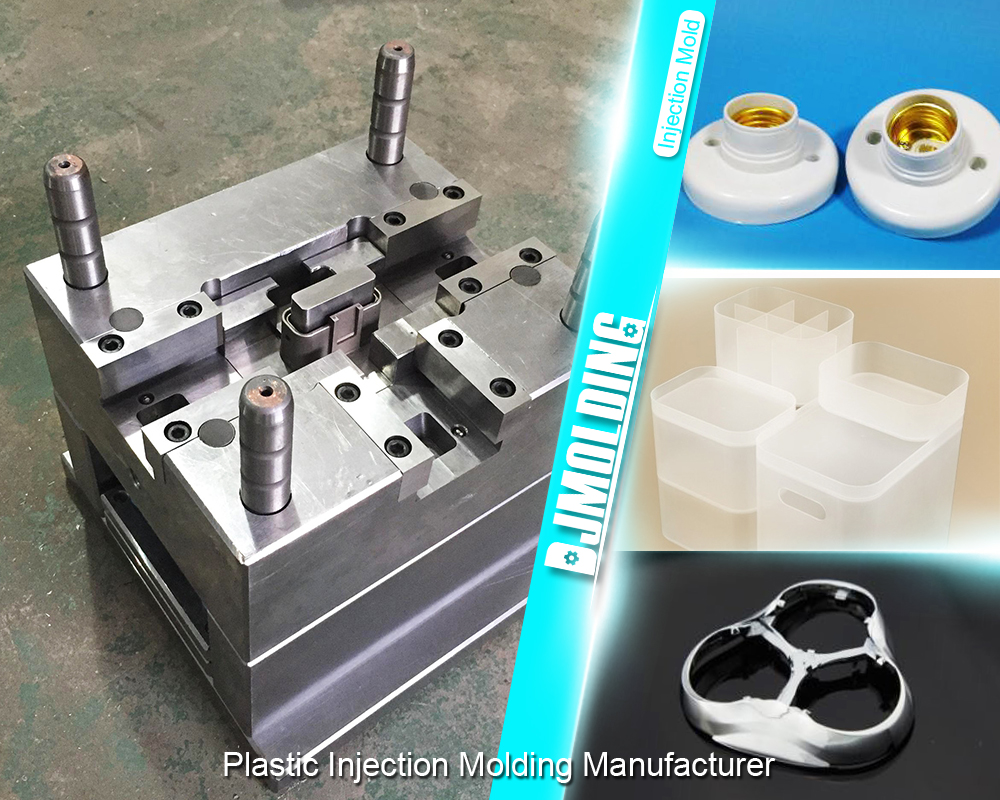
Understanding the Design Process of Plastic Injection Mold Assembly
The design process of plastic injection mold assembly involves several steps to ensure that the final product meets the desired specifications. The first step is to analyze the requirements and specifications of the product that will be manufactured using the mold. This includes determining the size, shape, and material of the product.
Once the requirements are established, the next step is to design the mold assembly. This involves creating a 3D model using computer-aided design (CAD) software. The design must take into account factors such as parting lines, draft angles, and gating systems to ensure proper injection and ejection of the plastic material.
During the design process, various factors need to be considered. These include the type of plastic material being used, the expected production volume, and any specific requirements or constraints. The design must also consider factors such as cooling systems, venting, and ejection mechanisms to ensure efficient and effective production.
Key Components of a Plastic Injection Mold Assembly
A plastic injection mold assembly consists of several key components that work together to shape and form the plastic material. These components include the mold base, cavity plate, core plate, ejector plate, and various inserts and pins.
The mold base is the foundation of the mold assembly and provides support for all other components. It is typically made of steel or aluminum and is designed to withstand the high pressures and temperatures involved in the injection molding process.
The cavity plate and core plate are responsible for creating the desired shape of the product. The cavity plate forms the outer surface of the product, while the core plate forms the inner surface. These plates are precision-machined to ensure accurate and consistent molding.
The ejector plate is used to push the molded product out of the mold after it has solidified. It contains ejector pins that are activated during the ejection process. Inserts and pins are additional components that are used to create specific features or details in the molded product.
Materials Used in Plastic Injection Mold Assembly
Various materials are used in plastic injection mold assembly, each with its own properties and characteristics. The choice of material depends on factors such as cost, durability, and specific requirements of the product being manufactured.
Steel is commonly used for mold bases and plates due to its high strength and durability. It can withstand the high pressures and temperatures involved in the injection molding process without deforming or wearing out quickly. Aluminum is also used for mold bases, especially for smaller molds, as it is lighter and more cost-effective.
For inserts and pins, materials such as hardened steel or pre-hardened steel are often used. These materials provide the necessary strength and wear resistance to withstand repeated use.
The Role of Computer-Aided Design (CAD) in Plastic Injection Mold Assembly
Computer-aided design (CAD) plays a crucial role in the design process of plastic injection mold assembly. It allows designers to create detailed 3D models of the mold assembly, which can be easily modified and optimized before production.
One of the main benefits of using CAD in the design process is improved precision and accuracy. CAD software allows designers to create complex geometries and intricate details with high precision. This ensures that the mold assembly will produce products that meet the desired specifications.
CAD also enables designers to simulate the injection molding process, allowing them to identify potential issues or defects before production. This helps to reduce the risk of costly errors and ensures that the mold assembly is optimized for efficient and effective production.
The Assembly Process
The assembly process of plastic injection mold involves several steps to ensure that all components are properly fitted and aligned. The process begins with preparing the mold base by cleaning and inspecting it for any defects or damage.
Next, the cavity plate and core plate are installed onto the mold base. These plates are carefully aligned and secured using bolts or clamps. Inserts and pins are then inserted into their respective positions, ensuring proper fit and alignment.
The ejector plate is installed last, along with the ejector pins. This plate is designed to move freely within the mold assembly to facilitate the ejection of the molded product. Once all components are assembled, the mold is inspected to ensure proper alignment and functionality.
Quality Control Measures
Quality control is of utmost importance in plastic injection mold assembly to ensure that the final product meets the required specifications and standards. Various measures are taken to monitor and control the quality of the mold assembly.
One common quality control measure is dimensional inspection, which involves measuring critical dimensions of the mold components to ensure they meet the specified tolerances. This can be done using precision measuring tools such as calipers or coordinate measuring machines (CMM).
Visual inspection is also performed to check for any defects or imperfections in the mold components. This includes checking for burrs, scratches, or any signs of wear or damage. Any issues identified during inspection are addressed and corrected before production.
In addition to inspection, regular maintenance and cleaning of the mold assembly are essential to ensure its longevity and performance. This includes lubricating moving parts, replacing worn-out components, and cleaning out any debris or contaminants.
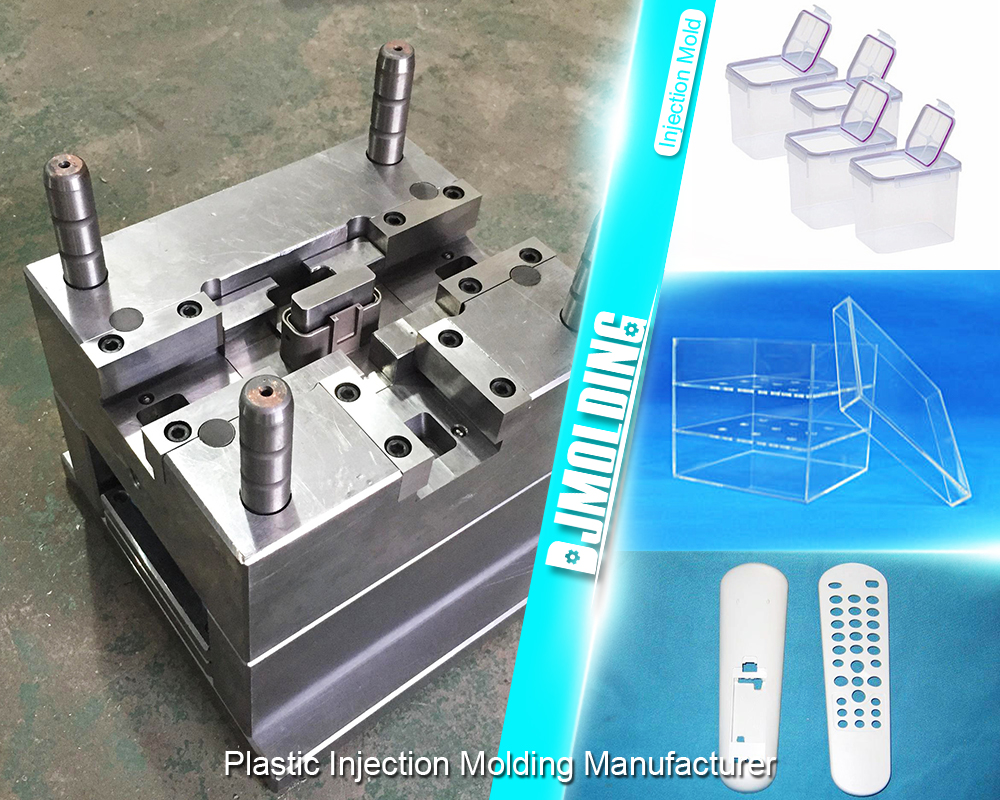
Last Words
In conclusion, plastic injection mold assembly is a complex and vital process that requires careful attention to detail and precision. By understanding the design process, key components, materials used, and the role of CAD, manufacturers can ensure the production of high-quality plastic products. With proper maintenance, quality control measures, and an eye towards future trends, plastic injection mold assembly will continue to play a crucial role in the manufacturing industry.
For more about the design and assembly process of plastic injection mold assembly in manufacturing,you can pay a visit to Djmolding at https://www.djmolding.com/ for more info.
The post The Design And Assembly Process Of Plastic Injection Mold Assembly In Manufacturing appeared first on Plastic Injection Molding Manufacturer.